For adverse geological conditions such as caves and fissures, gap filling and reinforcement are achieved by precisely controlling the diffusion range of slurry. For example, in broken rock formations, backfill grouting can prevent rock collapse and ensure construction safety.
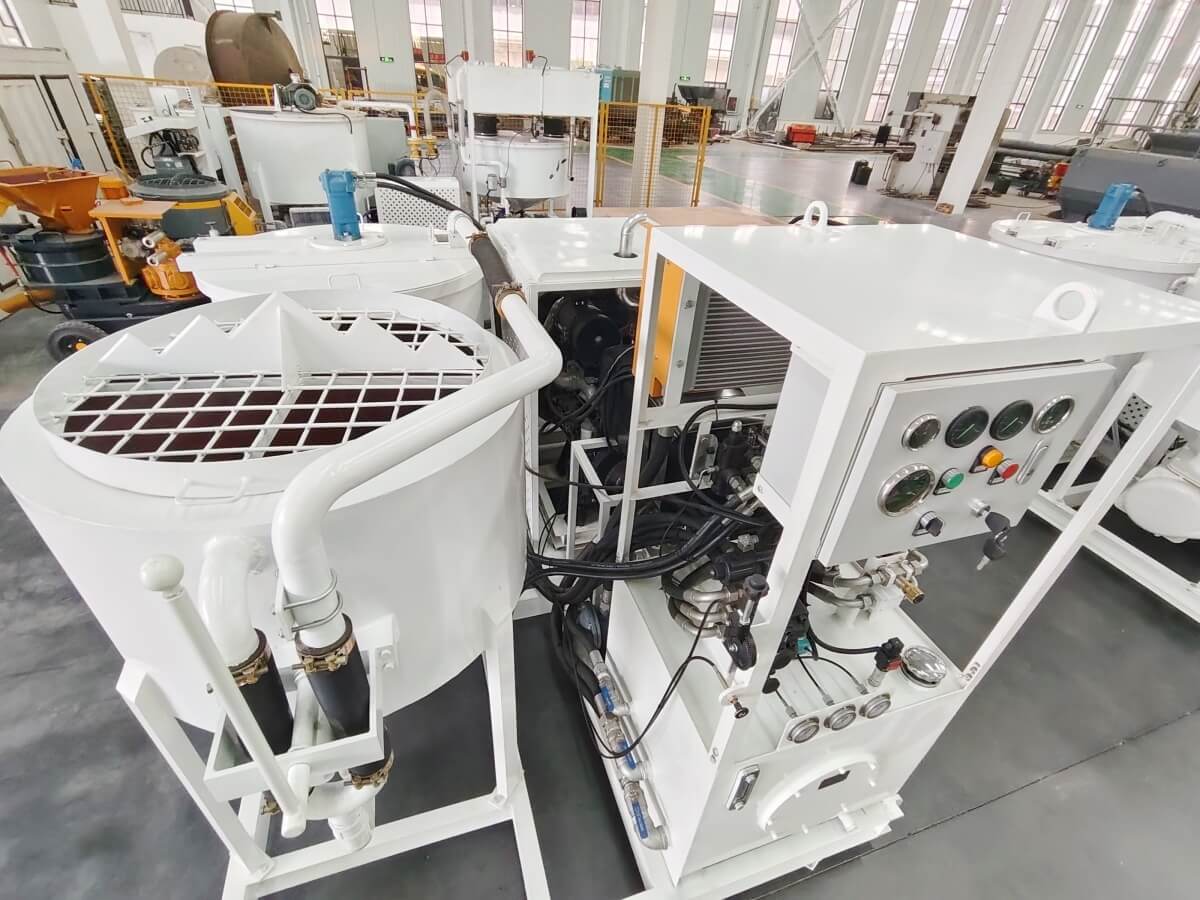
During the construction of a specific tunneling backfilling project, there are several core parameters that need to be controlled:
1. Grouting pressure
Design basis: Determined according to the thickness of the concrete lining, the reinforcement conditions and the stability of the surrounding rock.
Plain concrete lining: 0.2~0.3 MPa;
Reinforced concrete lining: 0.3~0.5 MPa;
Contact grouting (such as between steel pipes and concrete): needs to be determined through tests, generally not exceeding the safety pressure of the steel pipe against external pressure.
Adjustment principle: The initial pressure can be tested at 0.15 MPa, and dynamically adjusted according to the grouting situation to avoid excessive pressure causing structural damage.
2. Water-cement ratio and slurry ratio
Conventional ratio: The water-cement ratio decreases in four levels of 1:1, 0.8:1, 0.6:1, and 0.5:1. Cement mortar can be poured into the part with larger gaps (sand content ≤ 200% of cement weight).
Special scenarios:
Contact grouting: The water-cement ratio (weight ratio) of the slurry is (1-0.45):1. The larger the gap, the thicker the slurry;
Chemical grouting: For example, the volume ratio of water glass to cement is 1:0.5-1:1, which is suitable for small cracks or rapid coagulation requirements.
3. Diffusion radius and hole spacing
The diffusion radius needs to be determined through field tests. Generally, the initial grouting pressure is designed to be 0.3-0.45 MPa, and then adjusted according to the grouting volume.
Hole spacing: Designed according to the surrounding rock conditions, in typical cases, the borehole diameter is ≥38 mm, the hole depth is 10 cm into the rock, and the hole position deviation is ≤20 cm.
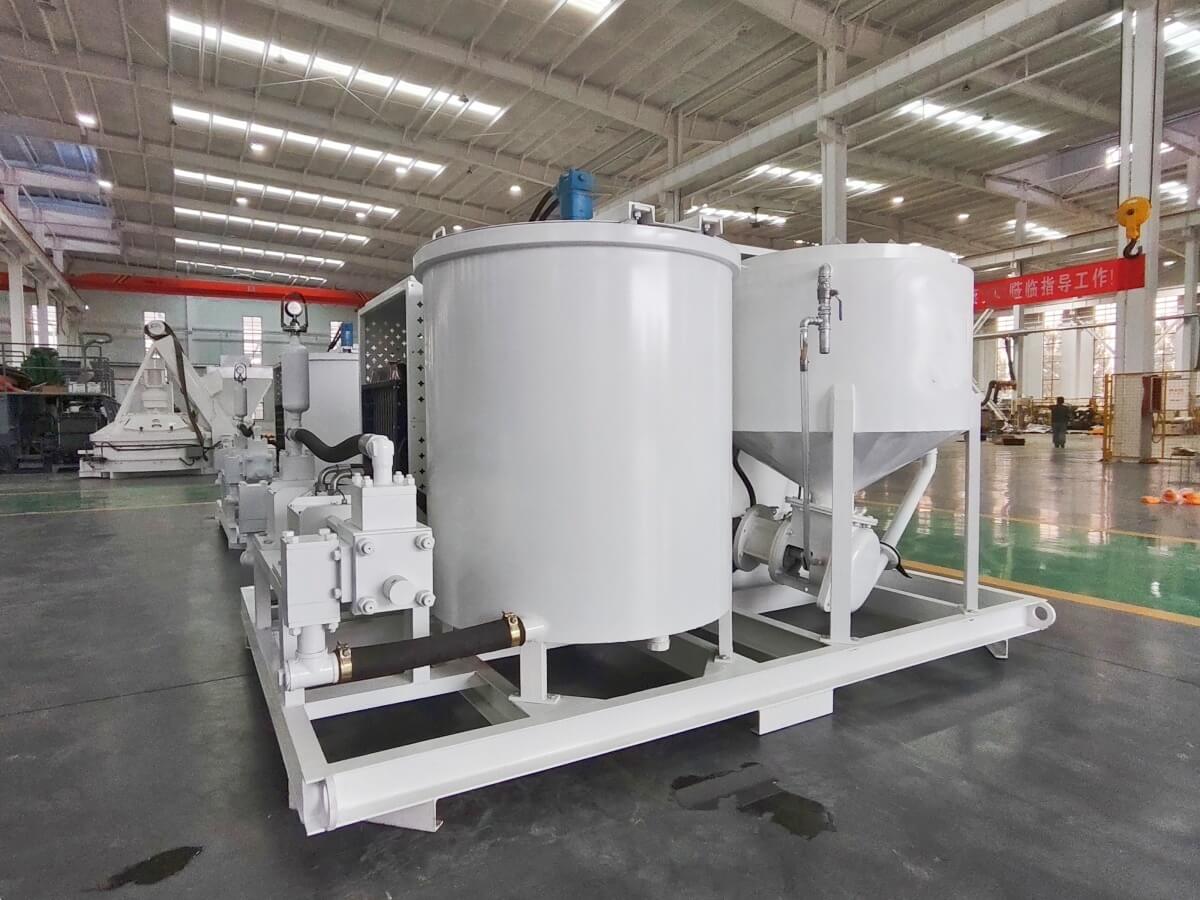
Grout plant used for tunneling backfill process optimization:
1. Construction preparation
Equipment inspection: Ensure that the grouting pump, mixer, pressure gauge and other equipment are in good performance and the grouting material is accurately weighed.
Hole location: Use the pre-buried pipe or the position designated by the supervisor to sweep the hole and remove the debris in the hole. The hole diameter is ≥50 mm.
Special treatment: The surrounding rock collapse, cave and other parts need to be pre-buried with grouting pipes (exhaust pipes), the number is ≥2.
2. Sequential construction
Two-sequence method: The interval between sequence I hole and sequence II hole is ≥48 hours. First grout the lower hole and advance upward layer by layer.
Single hole sequence: In the same section, a single hole can be drilled and then grouting can be performed, or concentrated grouting can be performed after all holes are drilled.
3. Grouting operation
Pure pressure grouting: It is completed by using a grouting pump, and the pressure is stabilized for 10 minutes until the grouting volume is 0.
Circulation grouting method: It is suitable for contact grouting. Single row is made into sequence I hole, double row is made into sequence II hole, and the sequence II hole is also used as an exhaust hole.
4. Sealing and acceptance
Sealing material: Use dry hard cement mortar or thick mortar to seal tightly, and press the hole mouth flush.
Acceptance standard: Quality inspection is carried out 7 days after the grouting is completed. The number of inspection holes is 5% of the total number of holes. The drilling grouting method (water-cement ratio 2:1) is adopted. The injection volume within the initial 10 minutes is ≤10 L to be qualified.
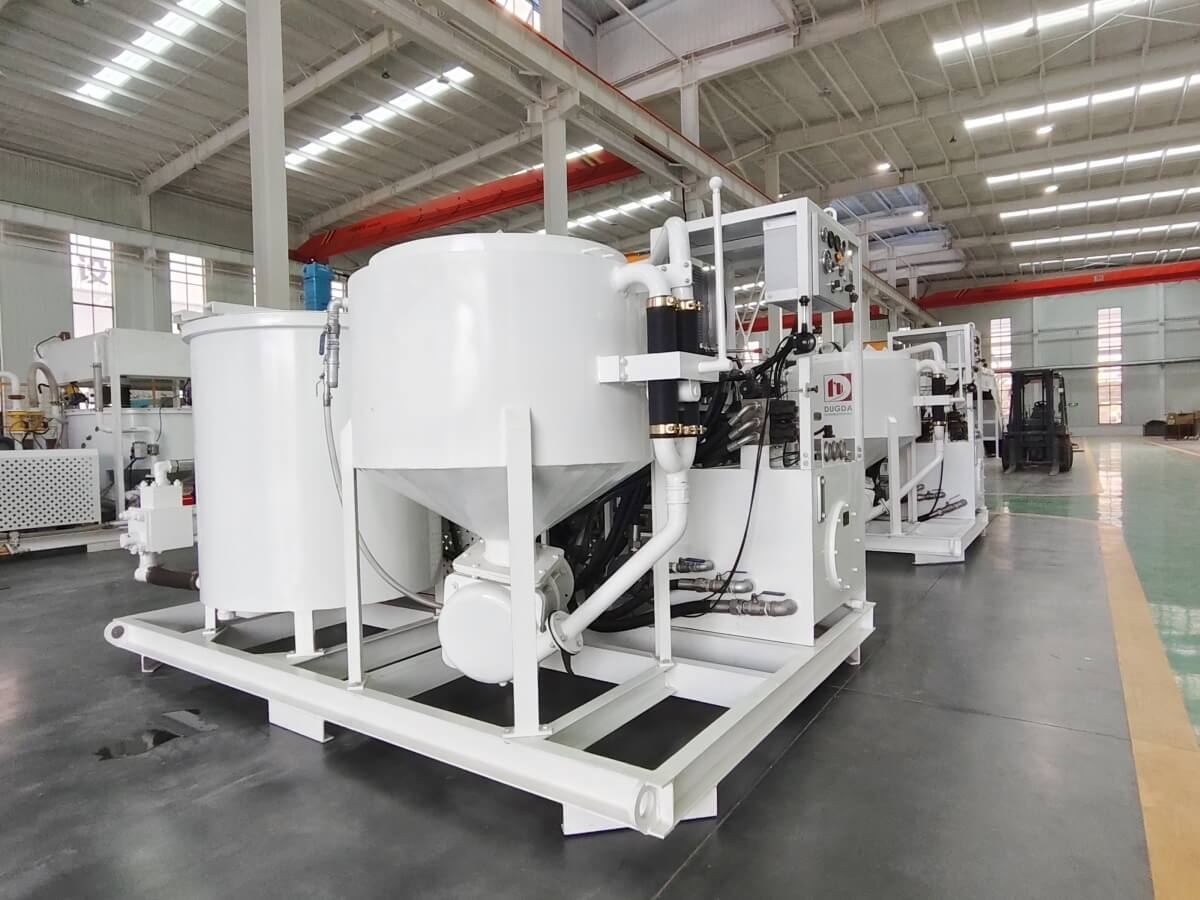
Material selection and performance requirements for tunneling projects using grout plant:
1. Cement-based grouting materials
Classification standard:
GB/T 50448-2015: According to fluidity, it is divided into Class I (cone fluidity ≤35 s) to Class IV (initial slump ≥650 mm);
Strength grade: 28-day compressive strength ≥50 MPa (Class I) or ≥60 MPa (Class II to Class IV);
Key parameters: vertical expansion rate 0.1% to 3.5% in 3 hours, water seepage rate 0%, chloride ion content <0.1%.
2. Chemical grouting materials
Applicable scenarios: small cracks, dynamic water environment or rapid setting requirements.
Typical ratio: water glass to cement volume ratio 1:0.5~1:1, or add accelerators (such as salt, triethanolamine) to shorten the setting time.
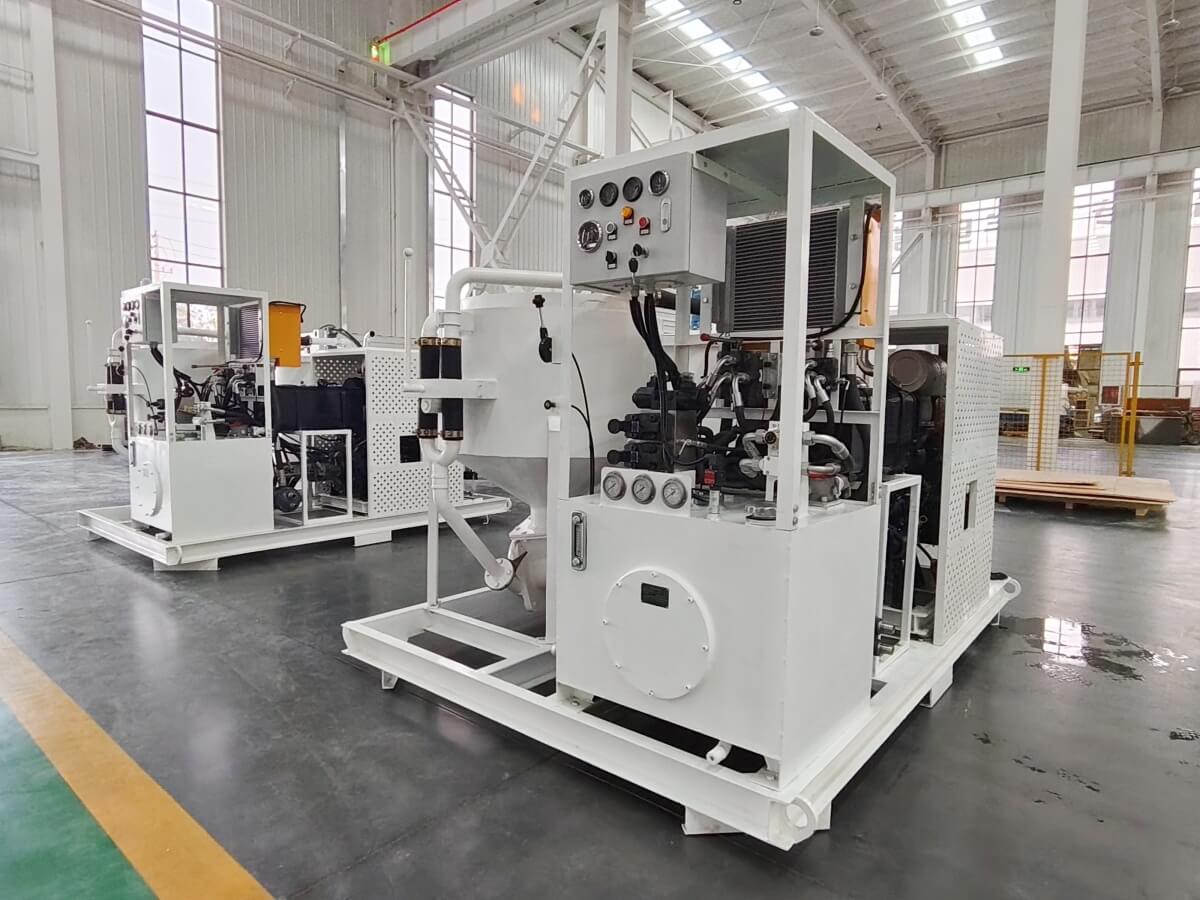
Quality control and risk prevention and control of tunneling backfill grout plant during construction:
1. Common problems
Grout leakage: construction joints, concrete defects and other parts need to be treated in advance, and the grout absorption volume should be monitored in real time during grouting.
Pipe wall instability: when contact grouting, a displacement meter is set to observe the deformation of the steel pipe and strictly control the grouting pressure.
Excessive water seepage: resulting in gaps between the grouting layer and the base layer, it is necessary to optimize the slurry ratio or add a water reducer.
2. Risk prevention and control measures
Technical training: Strengthen the skill assessment of construction personnel to ensure that they master key technologies such as sequential construction and pressure control.
Equipment update: Introduce advanced grouting pumps, mixers and monitoring instruments to improve construction accuracy and efficiency.
Emergency plan: Develop procedures for handling emergencies such as leakage and equipment failure to reduce downtime.