Container type cement and water mixing plant
Container type cement and water mixing plant cases: Tunneling/Mining: Grouting for ground stabilization or backfilling. Infrastructure Repair: Concrete production for bridges, roads, or dam. Disaster Response: Rapid deployment for temporary housing or emergency repairs. Soil Stabilization: Mixing cement/lime for soil improvement.
Container type cement and water mixing plant is a modular, pre-engineered system housed in a shipping container or similar enclosure. It’s designed for portability, rapid deployment, and efficient mixing of cementitious materials (e.g., cement, water, additives) for applications like construction, mining, tunneling, or disaster relief.
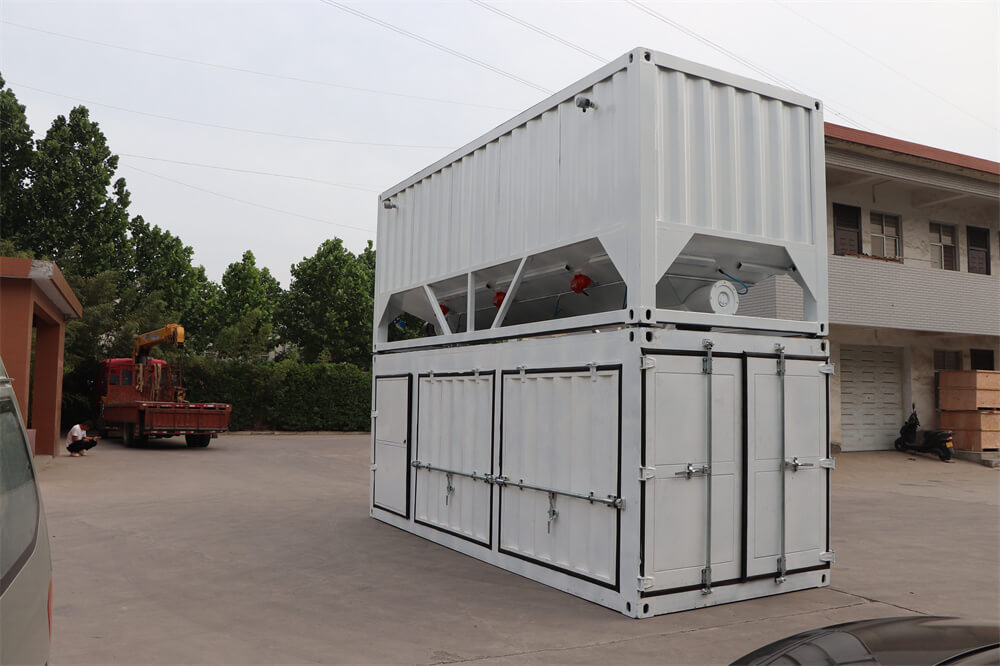
A container type cement and water mixing plant is a mobile, self-contained system designed for producing cementitious mixtures (e.g., mortar, grout, or specialized concrete) by combining cement, water, and additives in a controlled environment. Housed within a rugged container, these plants are engineered for portability, durability, and efficiency, making them ideal for remote or temporary construction sites.
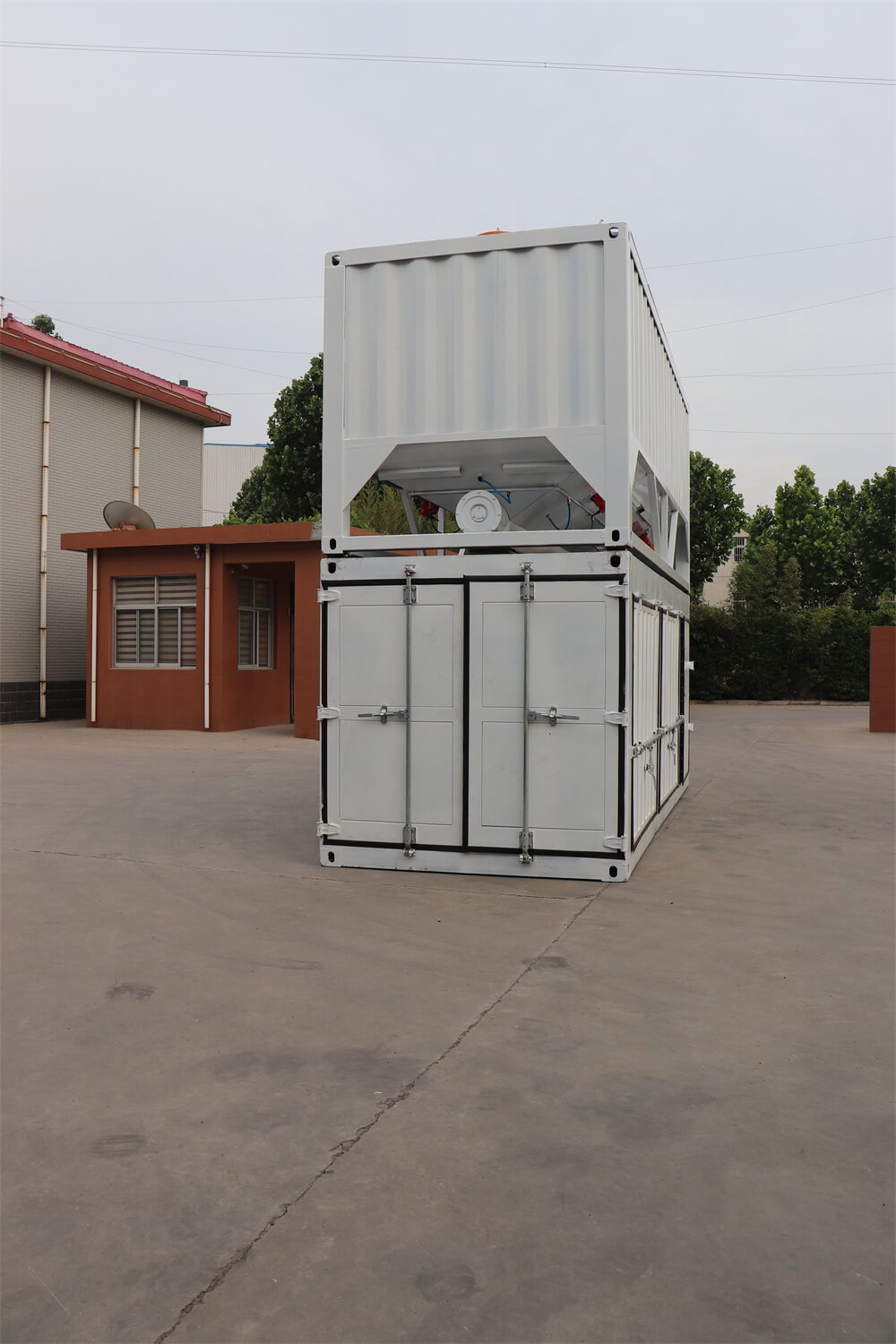
Container type cement and water mixing plant key features & design:
Containerized Structure:
Typically built into a steel shipping container or reinforced modular unit.
Protects equipment from weather, debris, and site conditions.
Includes storage silos for cement, water tanks, and additive compartments.
Mixing System:
High-capacity mixers (batch or continuous) with adjustable speeds.
Paddle, ribbon, or planetary mixers to handle various viscosities.
Optional automation for precise material dosing and mixing cycles.
Portability:
Mounted on trailers, skids, or truck chassis for easy transport.
Compact footprint for setup in confined spaces.
Some models include integrated pumps or conveyors for material delivery.
Efficiency & Flexibility:
Rapid setup and teardown between sites.
Modular design allows customization (e.g., additive systems, silos).
Dust suppression and spill containment systems for safety.
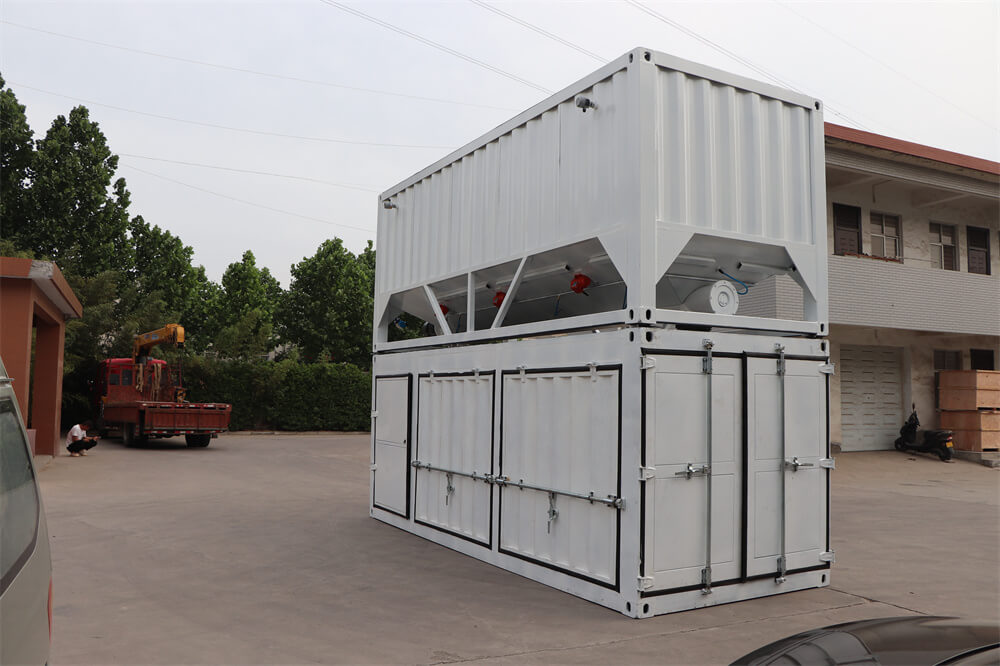
Advantages of container type cement and water mixing plant:
Mobility: Eliminates dependency on fixed batching plants.
Self-Sufficiency: Stores materials and water on-site.
Cost-Effective: Reduces waste and transportation costs for remote projects.
Durability: Built to withstand harsh environments and abrasive materials.
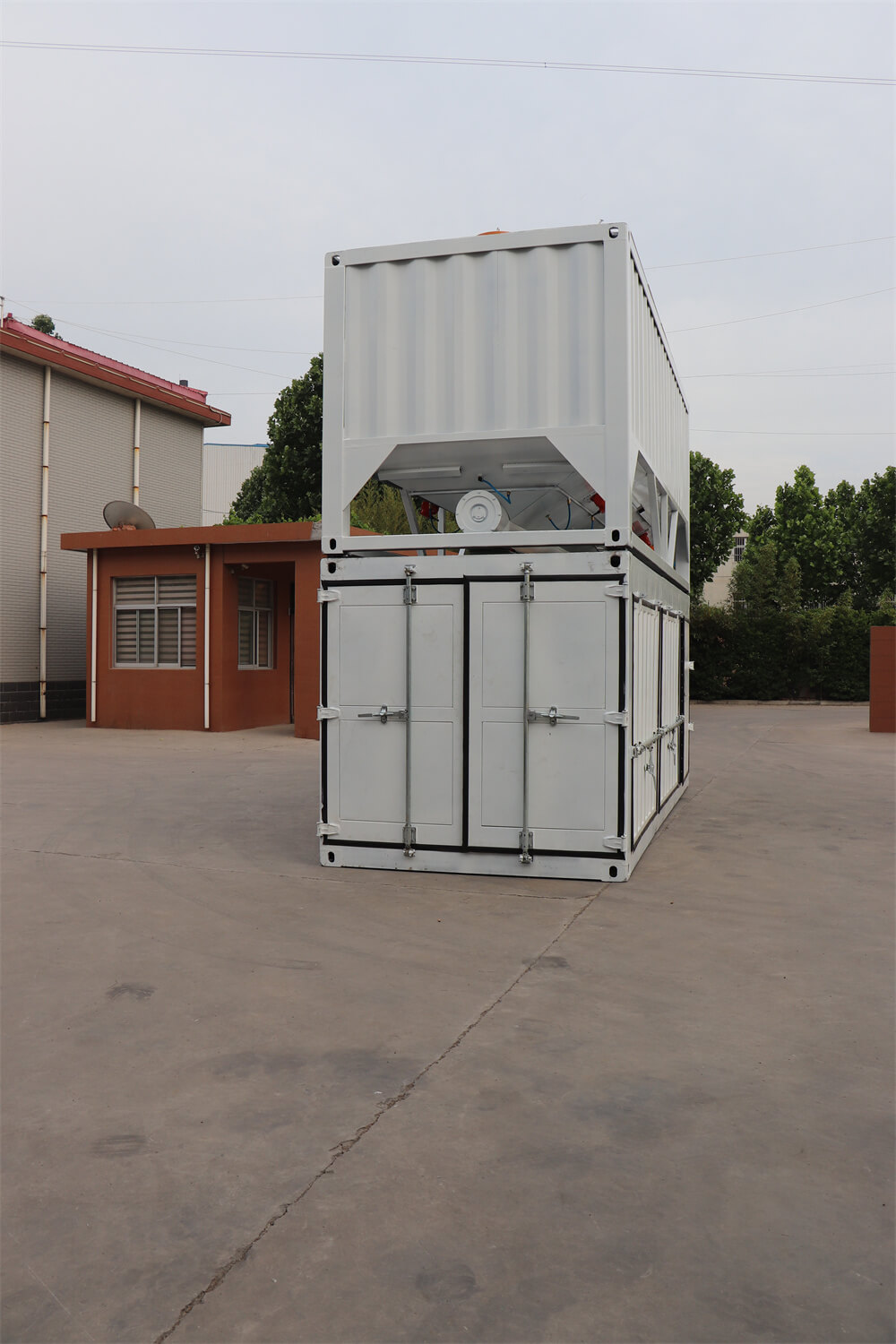
Types of container type cement and water mixing plant:
Batch Plants:
Mix one batch at a time; ideal for precise recipes or small volumes.
Continuous Mixers:
Produce material non-stop; suited for high-output applications.
Colloidal/High-Shear Mixers:
For fine-grained grouts or slurries (e.g., bentonite, cement-bentonite mixes).
Container type cement and water mixing plants offer a versatile solution for projects requiring on-demand, high-quality cementitious mixtures in remote or dynamic environments.