Big capacity container cement grout mixer
Big capacity container cement grout mixers are commonly used on construction sites, tunnel projects or any project that requires large quantities of cement slurry. This equipment is able to efficiently mix cement, sand, additives and water into a uniform cement slurry suitable for pouring into the ground or wall for reinforcement or other construction projects.
Big capacity container cement grout mixer is a specialized, portable mixing system designed for construction applications where grout (a mixture of cement, water, and additives) is needed. These mixers are typically housed in a rugged, self-contained container, making them ideal for remote or mobile worksites.
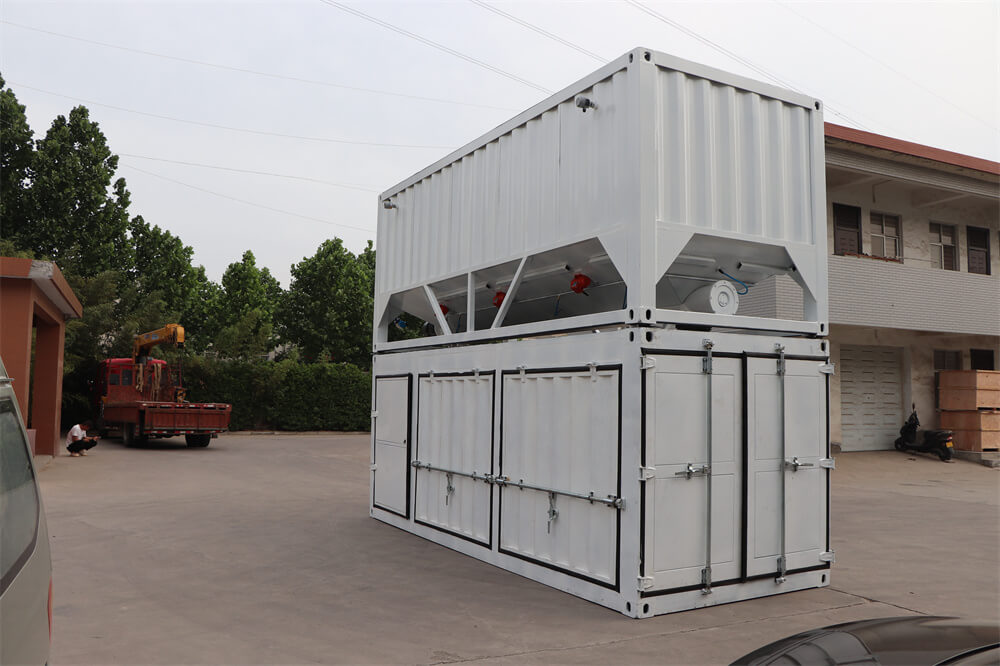
Applications of big capacity container cement grout mixer:
Underground Construction: Tunneling, mining, and shaft sinking.
Geotechnical Work: Soil stabilization, micropiling, and ground anchoring.
Civil Engineering: Dam repair, foundation work, and concrete repair.
Environmental Projects: Sealing landfills or contaminated sites.
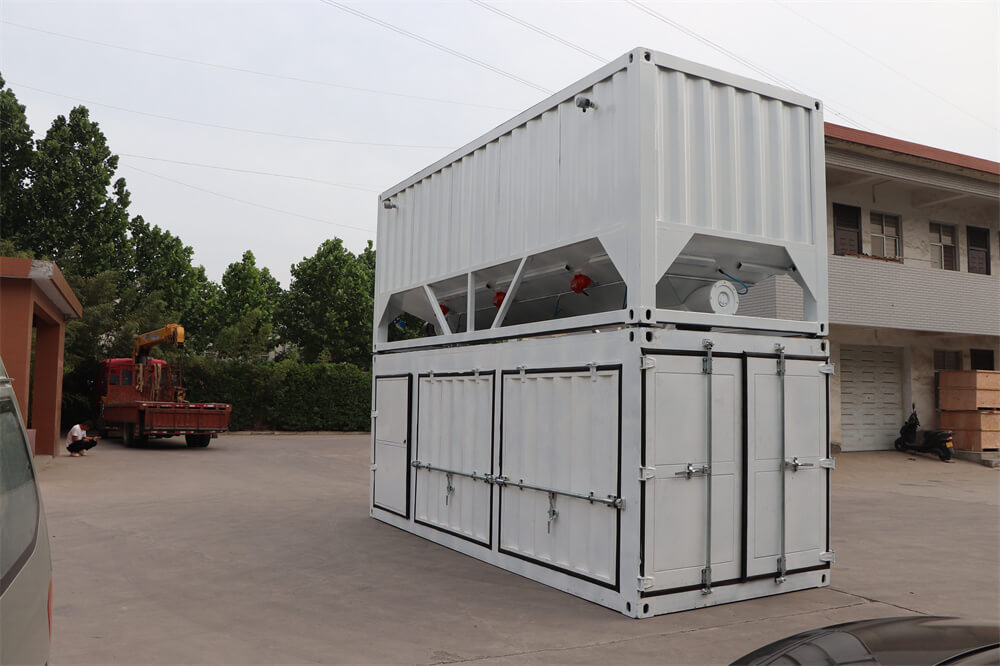
Advantages of big capacity container cement grout mixer:
Mobility: Quick setup and relocation between sites.
Self-Contained: Reduces reliance on on-site utilities.
Durability: Built to withstand harsh environments and abrasive materials.
Efficiency: Automated systems minimize labor and mixing time.
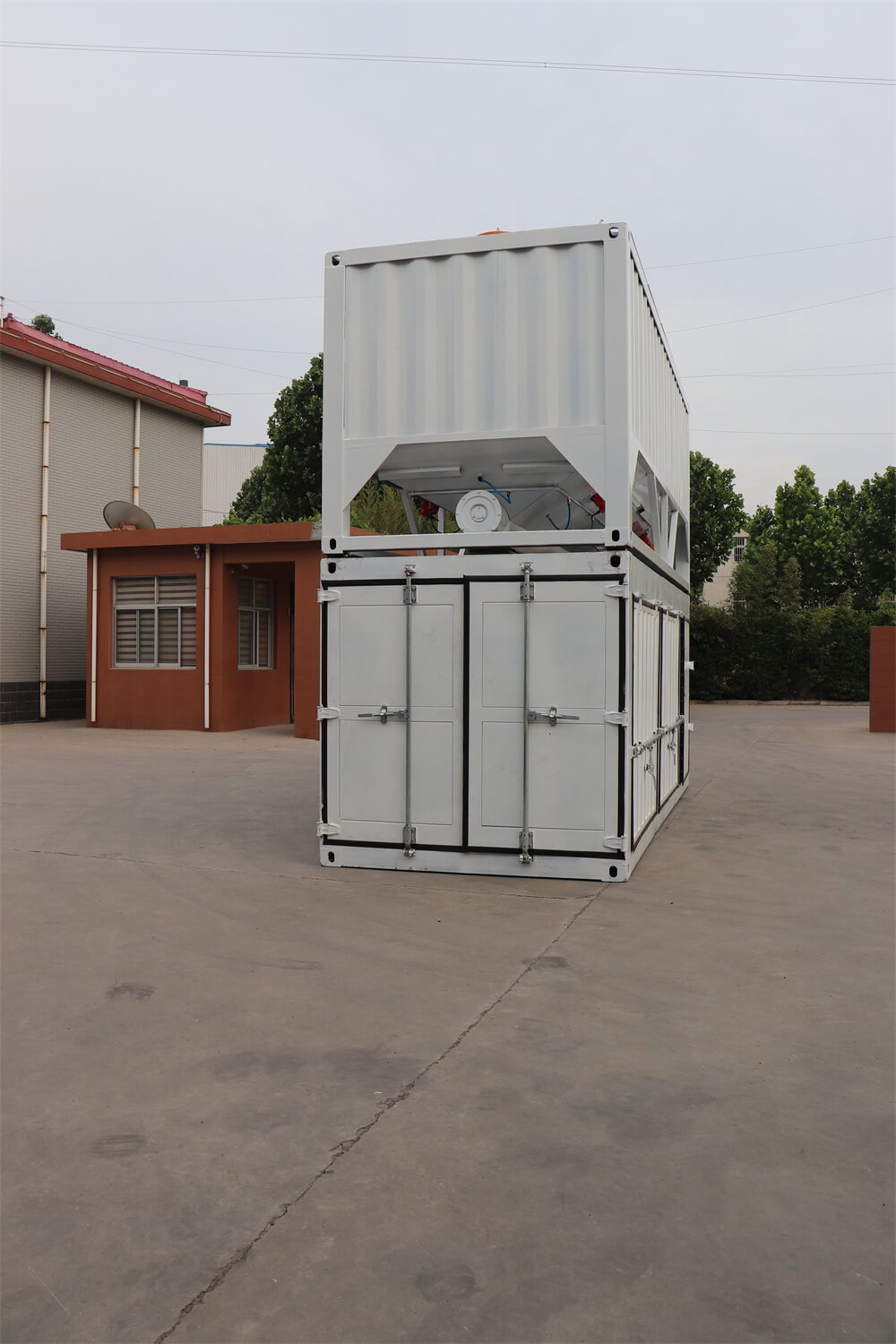
Any interest, please contact us by Email, sales@leadcrete.com