Compact cement grouting injection plant
A compact cement grouting injection plant is a specialized system designed for efficiently mixing and injecting cement-based grout into soil, rock, or concrete structures for purposes such as ground stabilization, foundation reinforcement, and waterproofing.
A compact cement grouting injection plant is a specialized system designed for efficient mixing and injecting cement-based grout into soil, rock, or concrete structures for purposes such as ground stabilization, foundation reinforcement, and waterproofing.
Applications of compact cement grouting injection plant:
Geotechnical Engineering
Soil stabilization for embankments, slopes, and retaining walls.
Ground improvement in liquefiable soils or weak strata.
Tunneling and Underground Construction
Rock bolting and pre-grouting to stabilize tunnel faces.
Waterproofing of underground structures.
Foundation Repair and Rehabilitation
Underpinning of sinking or cracked foundations.
Sealing of voids and fissures in concrete structures.
Mining and Dam Construction
Curtain grouting for seepage control in dams.
Rock mass consolidation in mining operations.
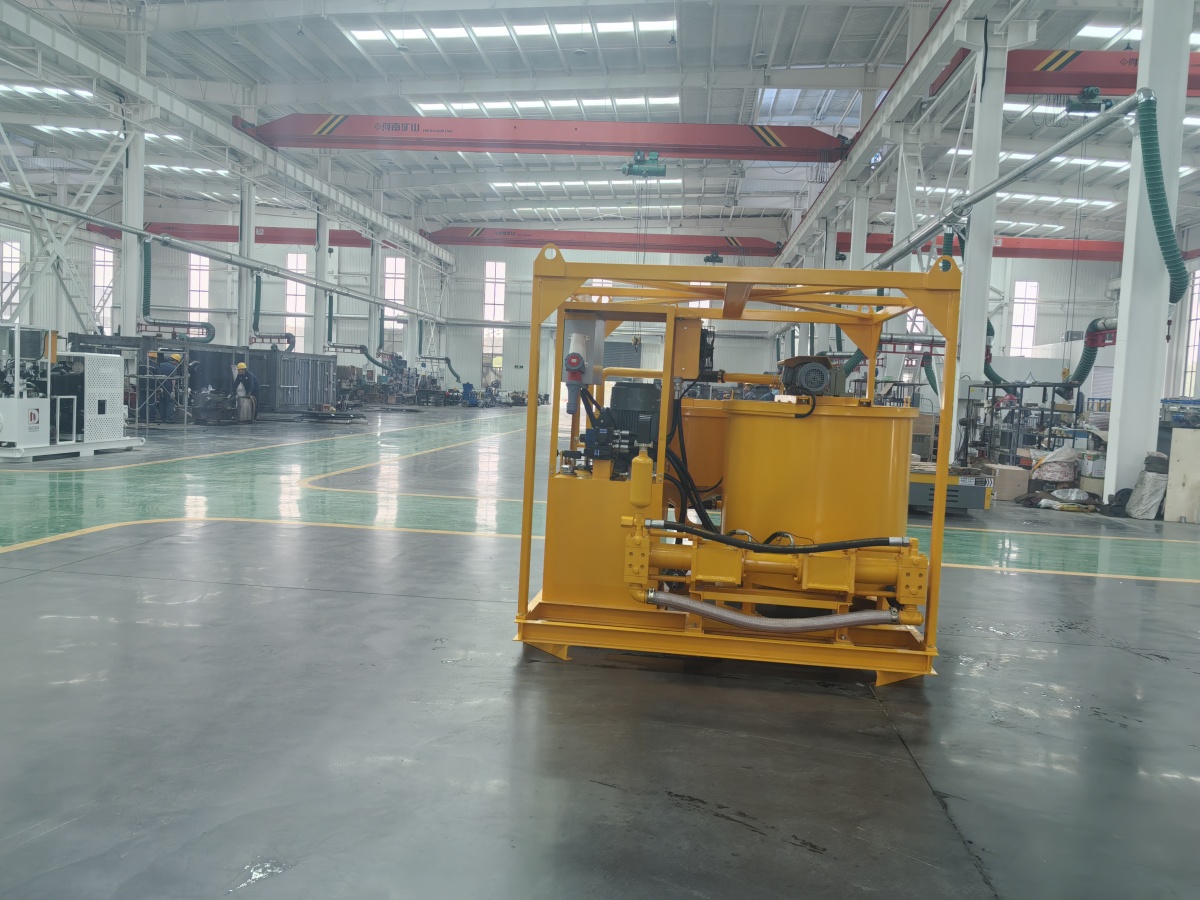
Advantages of compact cement grouting injection plant:
Efficiency: Automated mixing and injection reduce labor costs and improve productivity.
Precision: Accurate control of grout mix proportions and injection parameters ensure consistent quality.
Adaptability: Suitable for a wide range of soil types and engineering challenges.
Cost-Effectiveness: Minimizes material waste and maximizes grout penetration, reducing overall project costs.
Considerations for Selection
Project Scale: Larger plants may be required for high-volume projects, while compact units are ideal for smaller jobs.
Grout Type: The plant should be compatible with the intended grout mix (e.g., fine cement, microfine cement, or chemical grouts).
Mobility: For remote or difficult-to-access sites, a trailer-mounted or skid-mounted plant is preferable.
A compact cement grouting injection plant is a versatile and efficient solution for ground improvement and structural reinforcement projects. Its modular design, precision control, and adaptability make it suitable for various applications in civil engineering, mining, and environmental remediation. If you are considering purchasing a grouting pump station or would like more information, please contact us directly via email: sales1@leadcrete.com