Injection plant
Injection grout plant (grouting plant/grouting equipment system) is an integrated equipment system for grout preparation and injection in geotechnical engineering, construction and geological disaster management. Its core functions, technical features and application scenarios are as follows:
Core functions and equipment composition
Grout preparation system
Double-shaft mixer: adopts variable frequency speed regulation technology to achieve accurate proportioning of raw materials such as cement, water glass, bentonite, etc. (proportioning accuracy ±1%) to ensure slurry uniformity.
High-speed pulping machine: through the action of centrifugal force (speed ≥1450r/min), the powder is quickly dissolved, and the preparation efficiency is increased by 40% compared with traditional equipment, which is suitable for ultra-fine cement-based slurry.
Automatic batching system: integrated with screw conveyor, electronic scale and PLC controller to realize automatic metering and transportation of raw materials and reduce manual intervention.
High-pressure injection system
Piston pump group: adopts three-cylinder single-acting reciprocating pump (such as SGB6-10 type), with an output pressure of more than 10MPa and a flow rate of 6-10L/s, supporting single-liquid slurry and double-liquid slurry (cement-water glass) injection.
Intelligent control system: real-time monitoring of grouting pressure, flow and cumulative grouting volume, automatic generation of construction records (in compliance with GB/T 50448-2015 specifications), and support for cloud data storage and traceability.
Explosion-proof design: For high-risk environments such as coal mines, the equipment is equipped with explosion-proof motors, intrinsically safe circuits and pressure relief valves to ensure construction safety.
Injection grout plant application scenarios and cases
Foundation treatment and reinforcement
Soft soil foundation reinforcement: In the treatment of soft soil roadbed in coastal areas, high-pressure rotary jet grouting is used to form a composite pile with a diameter of 0.8-1.5m, and the bearing capacity of a single pile is increased by 200%-300%.
Existing building foundation support: Micro-pile grouting technology is used to complete the dense pile arrangement with a pile diameter of 0.3-0.6m in a small space, and the settlement control accuracy is ≤1mm.
Case: The foundation reinforcement project of the artificial island of the Hong Kong-Zhuhai-Macao Bridge uses a grouting plant to achieve an average daily grouting volume of 2000m³, shortening the construction period by 40%.
Geological disaster control
Landslide control: Cement-water glass double liquid slurry is injected into the landslide body in the southwestern mountainous area to form an integrated structure of anti-sliding piles and retaining walls, and the shear strength is increased by more than 50%.
Goaf filling: For coal mine goafs, high-flow grouting materials are used to fill the voids, reducing the surface settlement by 80% and ensuring the safety of surrounding buildings.
Case: In the geological disaster control project in the Wenchuan earthquake-stricken area of Sichuan, the grouting plant has completed a total control area of more than 500,000 square meters with a success rate of 100%.
Tunnels and underground projects
Advance support: Before excavating the tunnel in the water-rich stratum, a water-stop curtain is formed by grouting with a small advance pipe, which reduces the water inflow by 90% and significantly improves the construction safety.
Filling the voids behind the lining: Using radar detection and directional grouting technology, the voids behind the second lining are accurately filled, and the structural durability is improved by 30%.
Case: In the tunnel project of the China-Laos Railway, the grouting plant achieved an average daily advance of 15m on a single working face, and the construction period was advanced by 6 months.
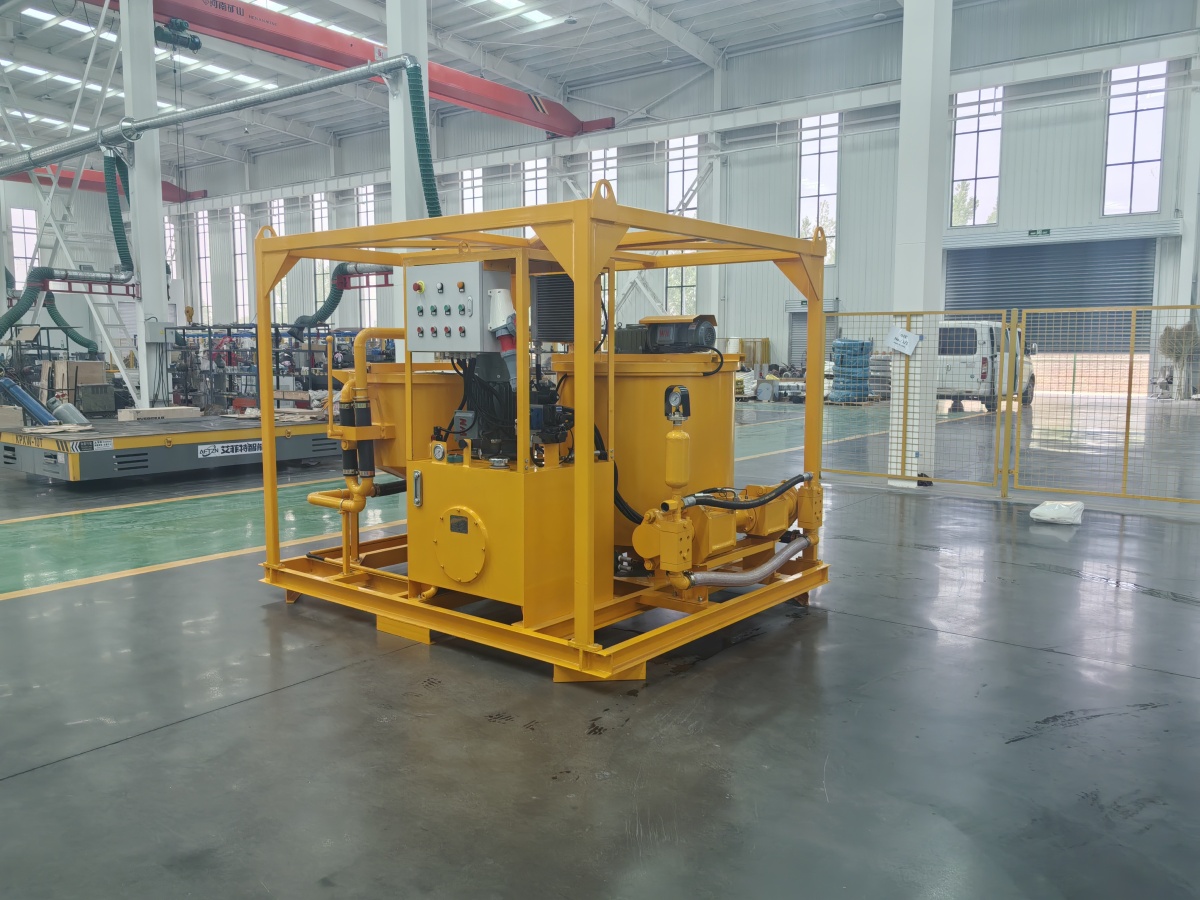
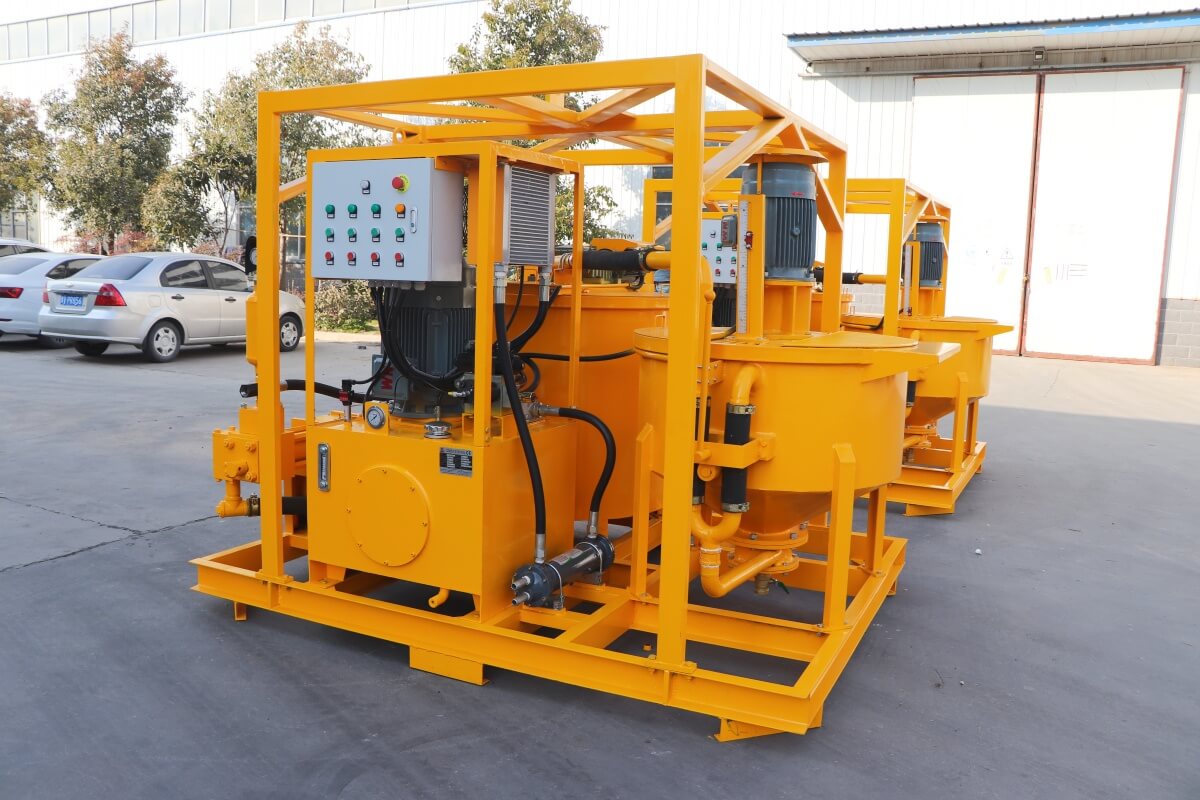
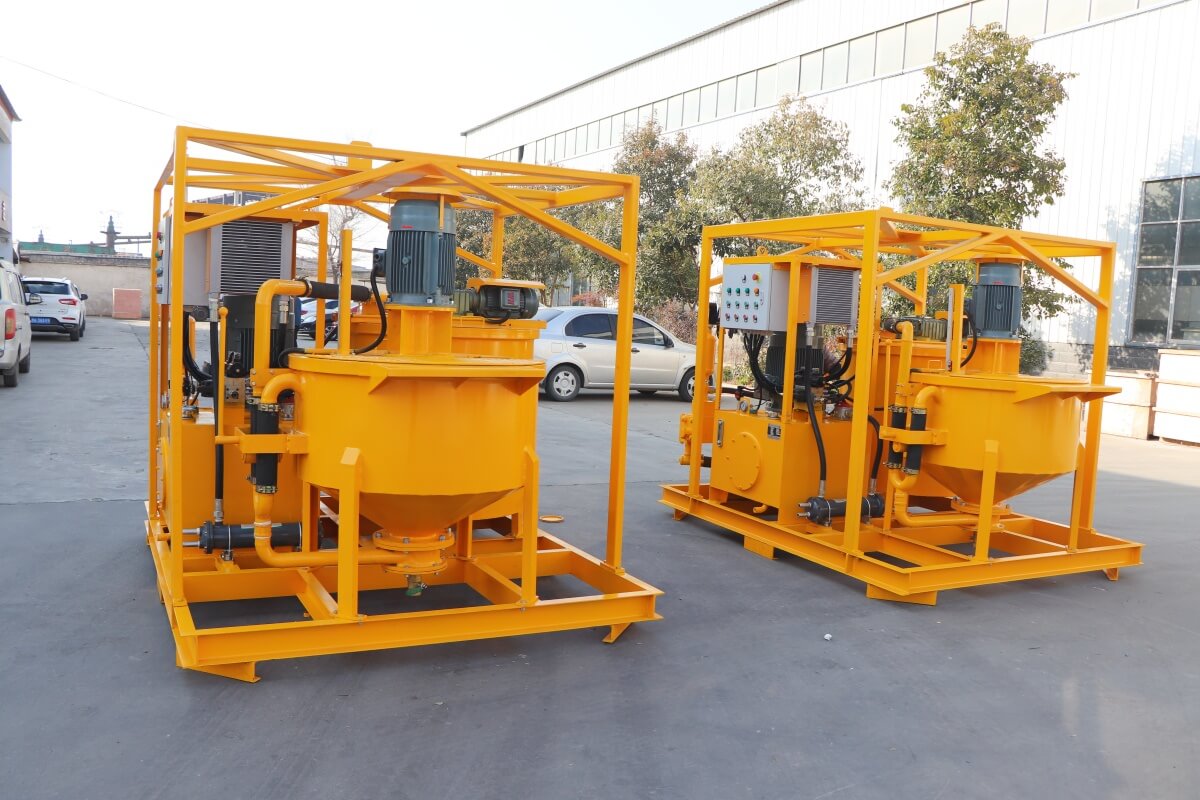
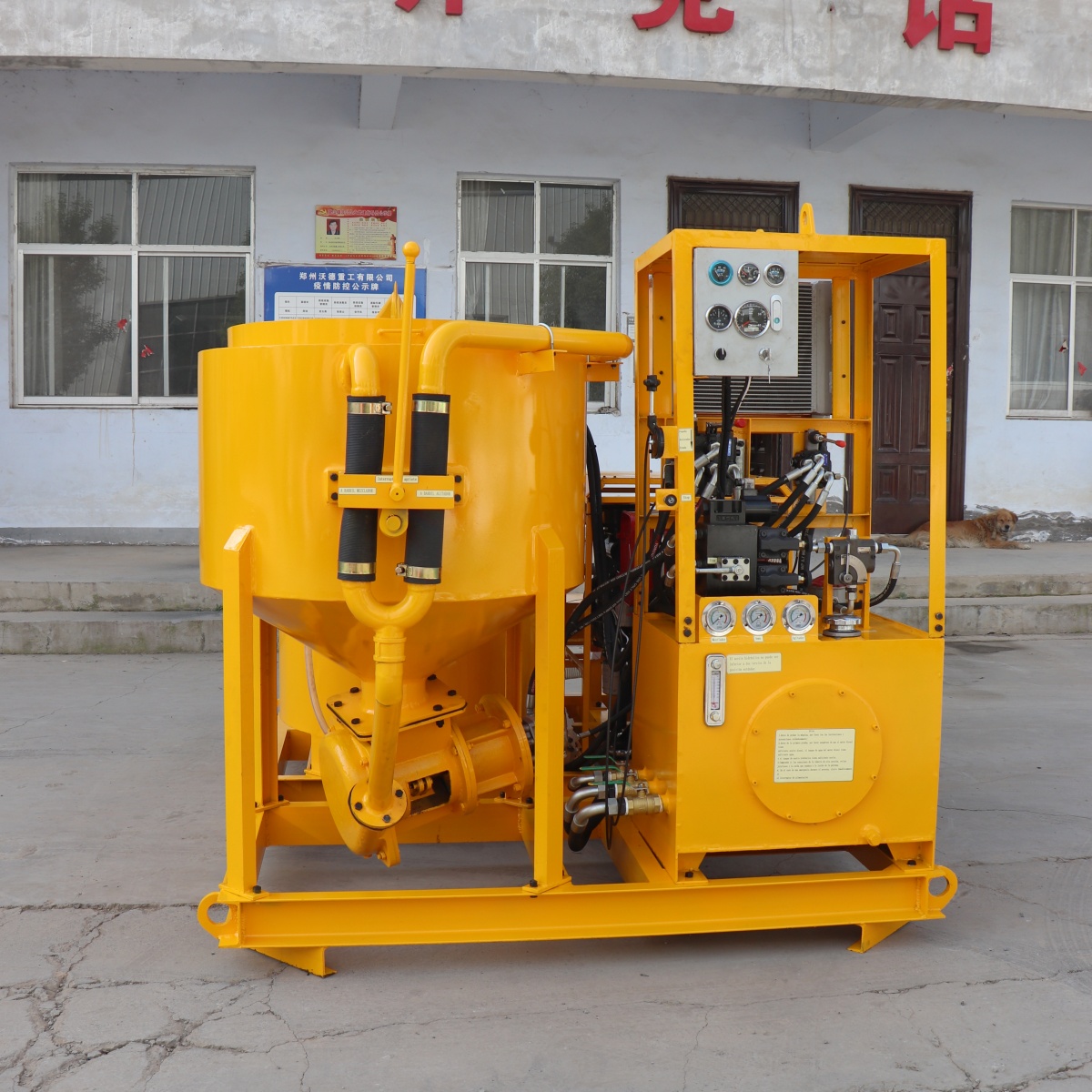
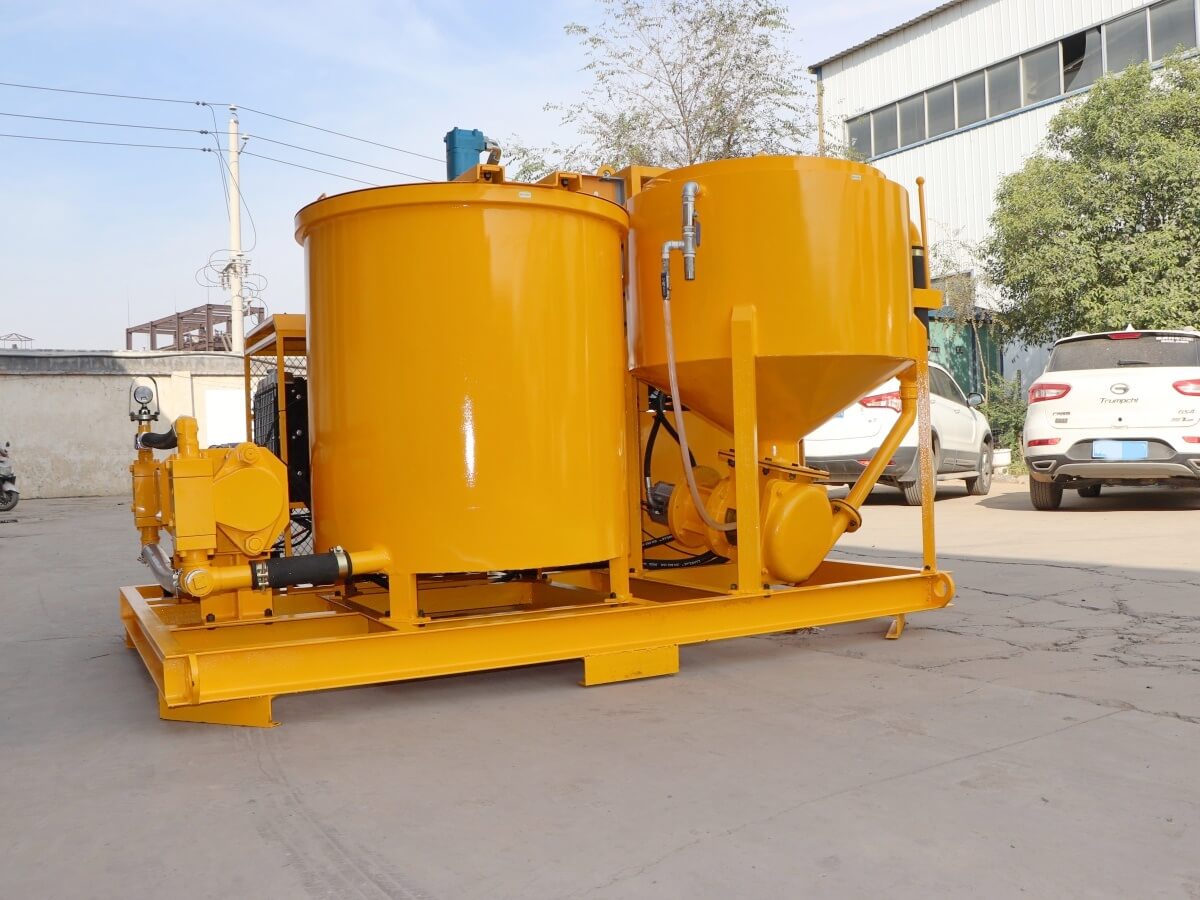
Technical features and advantages of injection grout plant
Full process automation
One-button start and stop: From raw material preparation to slurry injection, the whole process is automated and controlled, reducing labor costs by more than 30%.
Fault self-diagnosis: The equipment status is monitored in real time through sensors, and the machine automatically shuts down and alarms under abnormal conditions, with a fault response time of ≤5 minutes.
Remote operation and maintenance: Support 4G/5G modules to achieve remote monitoring of equipment status and parameter adjustment, and improve maintenance efficiency by 50%.
Modular design
Containerized integration: The size of the whole machine is suitable for 20-foot standard shipping containers, which is convenient for cross-border transportation and rapid on-site deployment (installation cycle ≤ 3 days).
Expandable components: Optional cement silos (30-100 tons), air compressor units, and generator sets form a complete mobile grouting station to adapt to working conditions without power/water sources.
Quick disassembly and assembly: With bolt connections and quick-plug connectors, the equipment transfer time is shortened to 1/3 of traditional equipment.