Foundation Grout Injection Plant
Foundation grouting stations are widely used in various projects that require grouting reinforcement, such as foundation grouting of buildings, bridges, tunnels, subways and other projects. It can effectively fill soil pores, improve the bearing capacity and stability of the foundation, and thus enhance the overall structural strength of the building. In addition, foundation grouting stations also play an important role in projects such as concrete structure reinforcement, crack repair and steel bar planting.
The foundation grout injection plant is a kind of equipment specially used for foundation grouting engineering. It can inject grouting materials (such as cement slurry, chemical grouting materials, etc.) into the gaps and holes of strata, rocks or structures under pressure to increase the bearing capacity, prevent leakage and improve the overall performance of the structure. The foundation grout injection plant usually consists of three main parts: mixing system, conveying system and grouting system, with the characteristics of high efficiency, automation and strong adaptability.
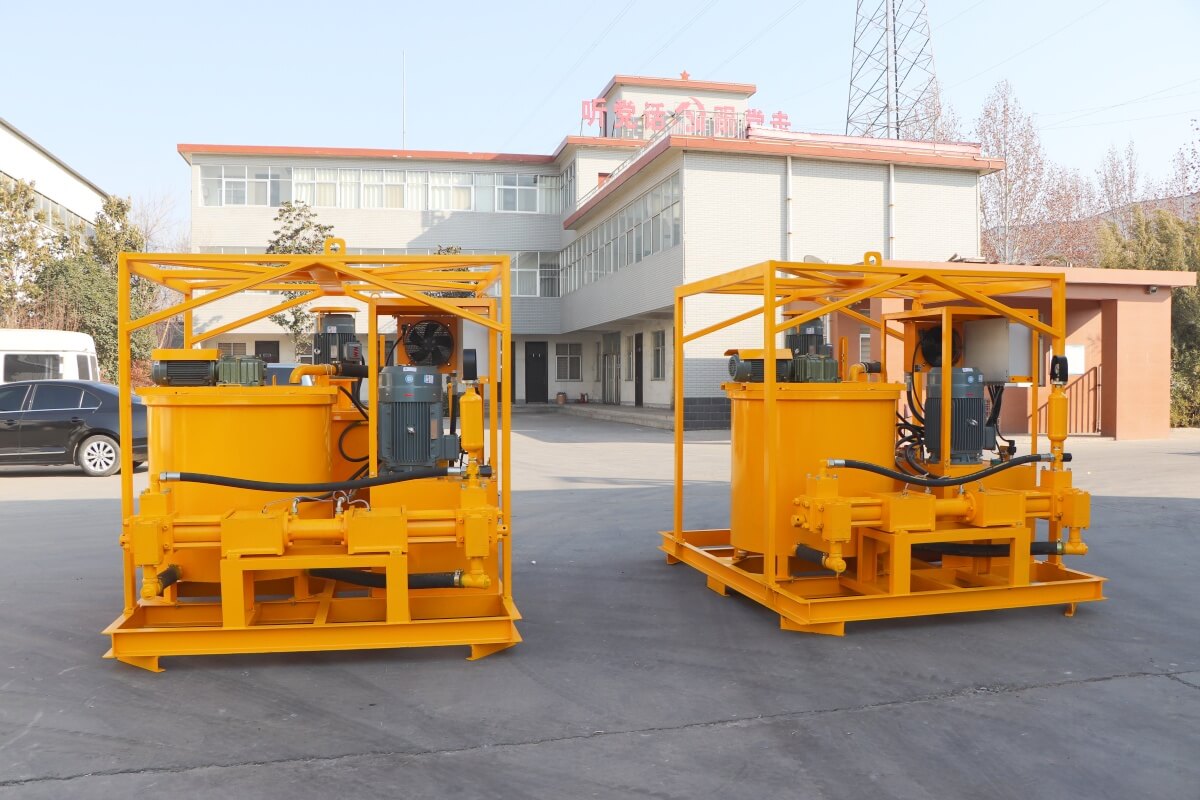
Foundation grout injection plant composition and function:
Mixing system:
Main function: uniformly mix grouting materials (such as cement, water, admixtures, etc.) to form grouting materials that meet the requirements.
Key components: agitator, mixing drum, motor, etc.
Features: high mixing efficiency, uniform mixing, and can ensure the quality of grouting materials.
Conveying system:
Main function: transport the mixed grouting materials to the grouting equipment through pipelines.
Key components: conveying pumps, conveying pipelines, etc.
Features: fast conveying speed and long conveying distance, which can meet the needs of different engineering environments.
Grouting system:
Main function: inject grouting material into the part that needs to be treated.
Key components: grouting pump, grouting pipe, pressure gauge, etc.
Features: high grouting pressure, high grouting accuracy, and can ensure the grouting effect.
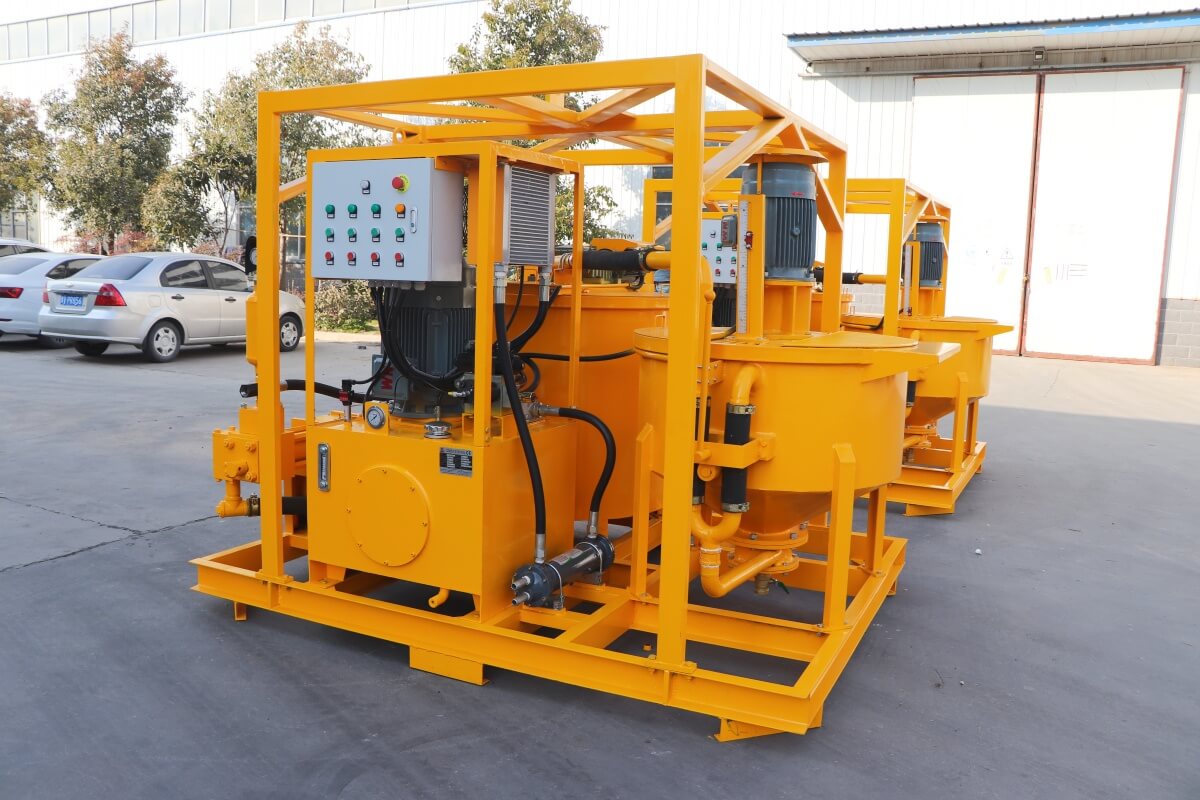
Application scenarios and advantages
Foundation grout injection plant application scenarios:
Foundation grouting of buildings, bridges, tunnels, subways and other projects.
Concrete structure reinforcement, crack repair, and steel bar planting and other projects.
Water conservancy projects, mines and other projects that require waterproofing and anti-seepage.
Foundation grout injection plant advantages:
Improve the bearing capacity of the foundation and enhance the overall structural strength of the building.
Prevent leakage and improve the waterproof performance of the structure.
The construction is simple, with little impact on the surrounding environment, and can effectively shorten the construction period.
High degree of automation reduces the difficulty and labor intensity of manual operation.
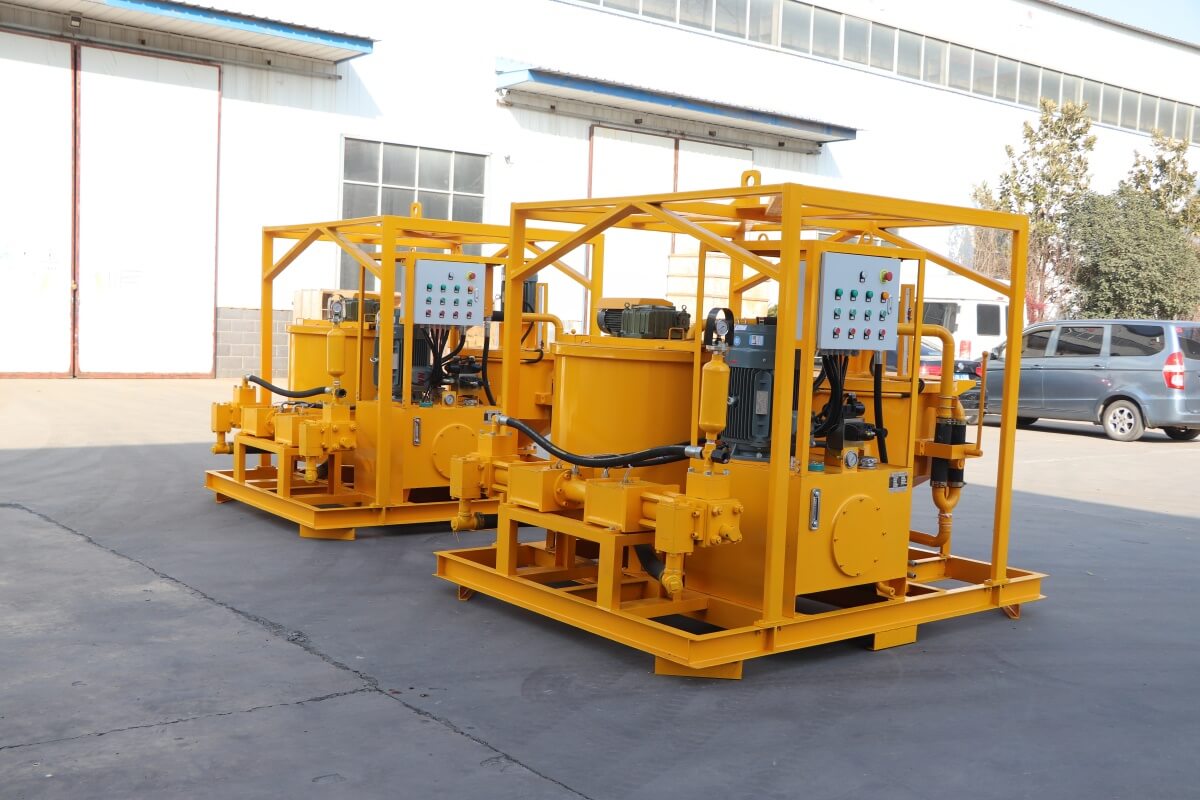
In summary, the foundation grout injection plant is an efficient, automated, and adaptable grouting equipment that has a wide range of applications in multiple engineering fields. When purchasing and using, it is necessary to select the appropriate equipment model and specifications according to project requirements, and perform regular maintenance and care to ensure its long-term stable operation.