Anchor injection grout plant
Anchor injection grout plant is a device or facility specializing in the production of anchor grout. In construction engineering, especially when it involves projects such as geotechnical engineering, tunnel engineering, basic reinforcement, etc., anchor rods are often used to enhance the stability of the structure.
Anchor injection grout plant is a grouting system specially used for anchor construction. After the cement, water, additives and other raw materials are mixed evenly, the grouting material is injected into the anchor hole through a high-pressure grouting pump, so that the grouting body is closely combined with the anchor rod body and the rock and soil body, thereby improving the tensile strength of the anchor rod. pull-out force and load-carrying capacity.
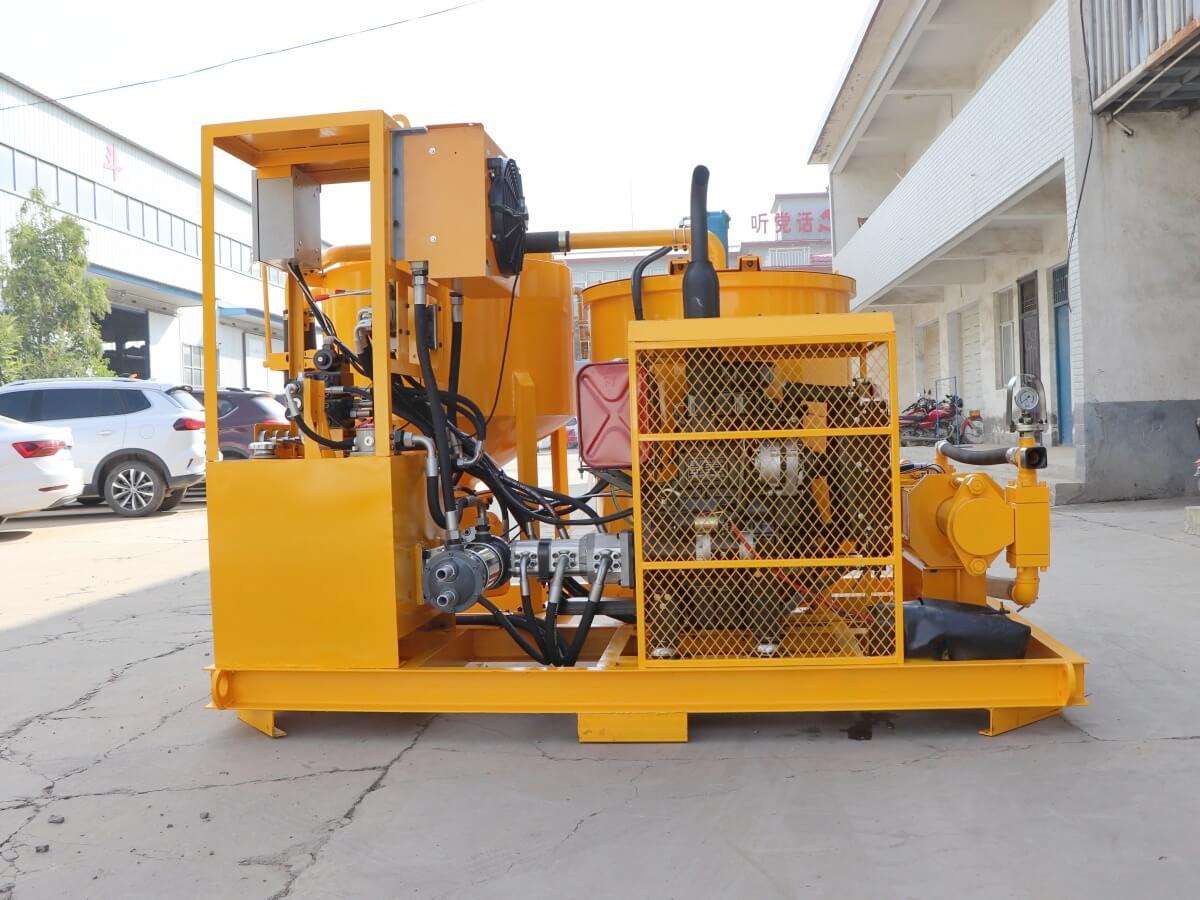
Anchor injection grout plant is widely used in various geotechnical engineering fields, such as tunnels, subways, slope support, foundation pit support, etc. In these projects, anchor grouting equipment can significantly improve the anchoring effect of the anchor and enhance the stability and load-bearing capacity of the rock and soil mass.
The working principle of anchor injection grout plant is as follows:
First, add cement, water, additives and other raw materials into raw material storage tanks respectively.
The amount of each material is then accurately metered through a control system and fed into the mixing system.
In the mixing system, the raw materials are fully stirred and mixed evenly to form grouting materials that meet the requirements.
Then, the grouting material is sent to the high-pressure grouting pump and injected into the anchor hole through the grouting pipeline.
During the grouting process, the control system monitors and adjusts grouting pressure, grouting speed and other parameters in real time to ensure grouting quality and safety.
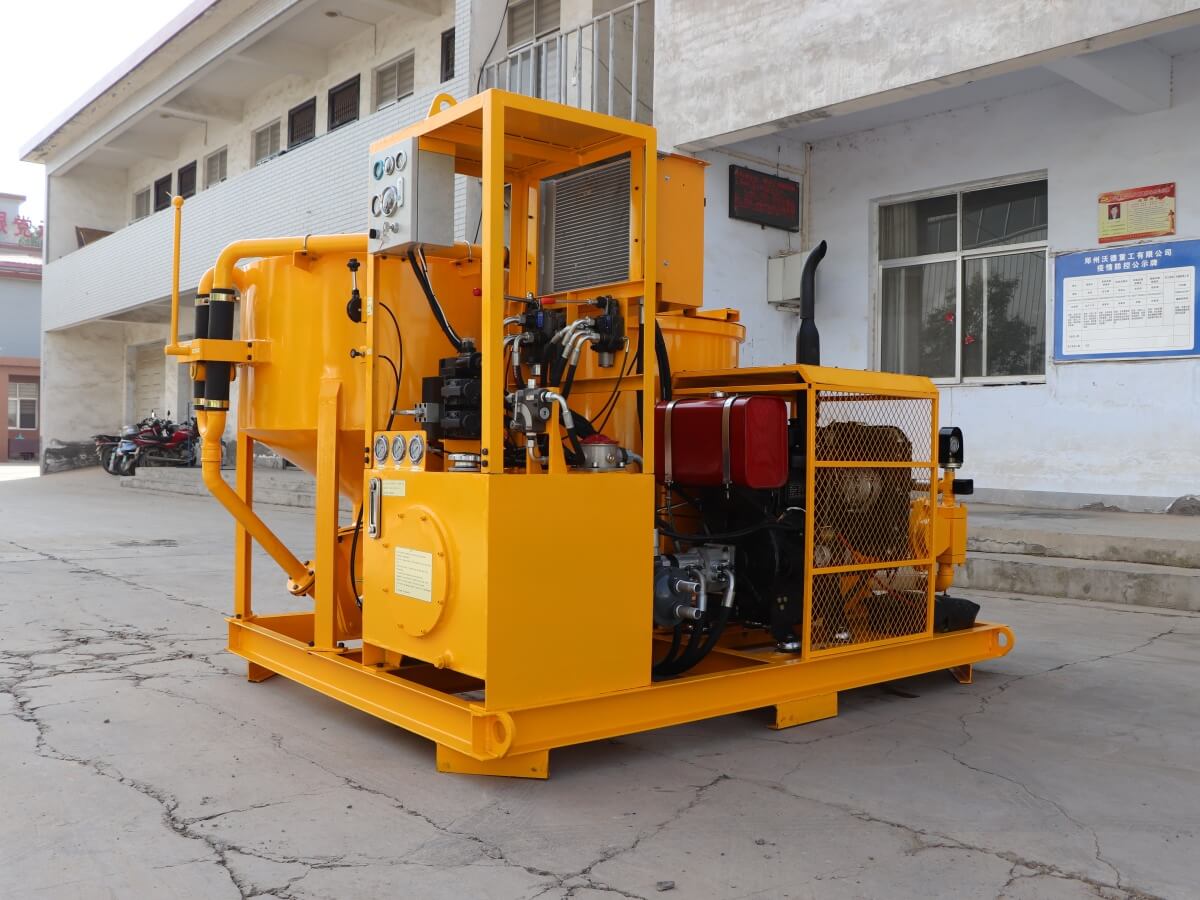
Anchor grouting injection plant usually consists of the following main parts:
Raw material storage and measurement system: used to store raw materials such as cement, water, additives, etc., and accurately measure the amount of each material.
Mixing system: Mix the measured raw materials evenly to form grouting materials that meet the requirements.
Grouting system: including high-pressure grouting pump and grouting pipeline, used to inject mixed grouting materials into anchor holes.
Control system: Control and monitor the entire grouting process to ensure grouting quality and safety.